How position measurement affects 5-axis machining accuracy
The benefits of position measurement with HEIDENHAIN linear and angle encoders are evident on a Telstar workpiece. For flawless appearence of the Telstar ball, its grooves, pentagons, and hexagons must be milled to high precision during over two hours of machining. Due to the programmed angle of the cutter relative to the workpiece, the rotary and linear axes make expansive movements. This necessitates a high volumentric accuracy.
Semi-closed loop control
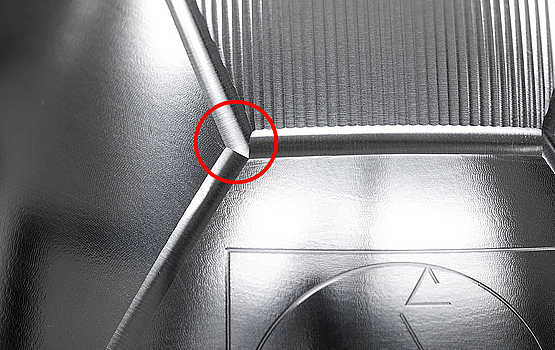
Closed loop control

Sustained accuracy in small- and medium-batch production
The capability of a machine tool to cope with rapidly changing operating conditions is a decisive factor for its accuracy. A transition from roughing to finishing completely changes the mechanical and thermal load on the machine, which can cause considerable changes in accuracy. Similar load changes occur during machining of smaller production runs. Permanent changes between setup processes and order-specific machining cause varying heat inputs with the corresponding effects on accuracy
Greater accuracy for machining centers in automated large-batch production
Serial production in the automotive industry is currently changing. Rigid transfer lines for drivetrain components, for example, are being replaced by lines of linked machining centers for greater flexibility.
The dimensional accuracy of finished parts depends on the individual machines and subprocesses of the entire production system. Linear encoders in closed loop configurations help increase the machining accuracy. Greater tolerance reserves, for example, can then be used to deploy tools for longer periods.